Blast Pro Blog Keep up to date with all the latest news from the team at Blast Pro!
4 Reasons to Choose 2 Pack Paints for Earthmoving Equipment
What are 2 pack paints?
Why is 2 pack paint suitable for earthmoving equipment?
Why Use Dustless Sandblasting
How does dustless sandblasting work?
What are the advantages of dustless sandblasting?
Garnet Sand Blasting & Its Applications
What is garnet sand?
Where does garnet sand come from?
What applications do technicians use garnet sand for?
Garnet sand works as a surface preparation and cleaning abrasive. This makes it ideal for a wide range of industrial applications, including the following:
- Aluminium surfacing
- Anti-magnetic steel preparation
- Fibre glass surfacing
- Glass etching
- Glass polishing
- Speciality metal alloy surfacing
- Stainless steel preparation
- Turbine blade surfacing
- Water filtration
- Wood finisher
Because garnet sand contains no metal, various industries approve it for use. Garnet sand represents one of the most common abrasives used by major oil companies, large factories and industrial plants and ship yards.
Why do technicians use garnet sand?
How does garnet sand blasting compare to other types?
Garnet sand is environmentally inert and meets most health and safety requirements. In recent years, this means it has begun to replace other sand blasting materials. Materials like silica, aluminium oxide and steel slag emit toxins and create high levels of dust. This makes them a breathing hazard for industrial workers.
While silica still represents the most common abrasive in most countries, Germany, Belgium, Sweden and the United Kingdom have banned its use. These bans resulted from links between silica use and operator lung disease.
Garnet sand costs somewhat more than silica, which is why it remains less common. However, garnet sand poses little to no health risk as it does not produce excess dust during use.
If you or your company require a sand blasting service, talk to your technician about garnet sand for your next project. This environmentally friendly option can decrease costs and increase efficiency in sand blasting tasks for many industries.
Consider the characteristics discussed above when deciding whether garnet sand is the right abrasive for your specific application.
Getting in Touch with Our Artistic Side!
Our client Swan Fabricators www.swanfab.com.au have been involved in the fabrication of some metal artworks for the Reveley estate at Ellenbrook for LWP.
Article: http://www.lwppropertygroup.com.au/…/new-11m-sculpture-form…
These photos show some of the intricate sandblasting work we have undertaken. The finish on the non polished areas has to be carefully blasted to ensure an even profile, There is a lot of masking involved and a special stand had to be made to allow the ball to be rotated during blasting. Also shown is a clam shell that we blasted prior to it going to be polished.
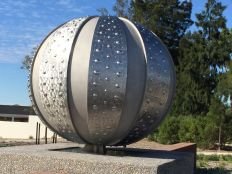
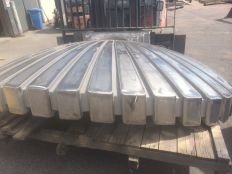
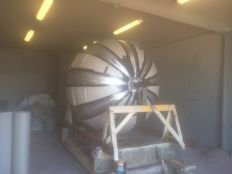
